Eyewear sampling is the process of physically verifying eyewear design before mass production. This process is critical as it helps eyewear buyers, manufacturers and designers check the design’s feasibility, comfort and appearance. The basic process of eyewear sampling is roughly as follows:
1. Design Confirmation
The designer or client first provides the design drawing or 3D model of the glasses, based on CAD, AI, CorelDRAW, 3ds Max, etc…
Confirm material specification, size, color and other details.
Product specifications:
- Colors: (black, grey, transparent, neon, red, hawksbill…)
- Process (electroplating, lamination, seamless welding, injection molding, baking time…)
- Lens (TAC, AC, PC, glass, polaroid, trivex, CR39, nylon…)
- Material (acetate, Aaloy, stainless steel, titanium, PC, carbon fiber… )
- Screw Type (metal, nylon…)
- Hinge Type (metal, with screws, without screws, patented hinges, reverse R hinges, memory materials, flexible materials…)
- Nose Pad Type (plastic, metal, silicone, titanium, celluloid, ceramic… )
- Logo (Mould stamping, metal sticker, zinc alloy trims, laser, hot stamping, tamper evident labels…)
- Certification (BSCI, CE, FDA, GMP, GRS, ISO9001, ISO13485, ISO14001, UKCA…)
2. Data Processing
Convert design drawings or 3D models into a data format suitable for reading by machining equipment, such as STL or DXF files.
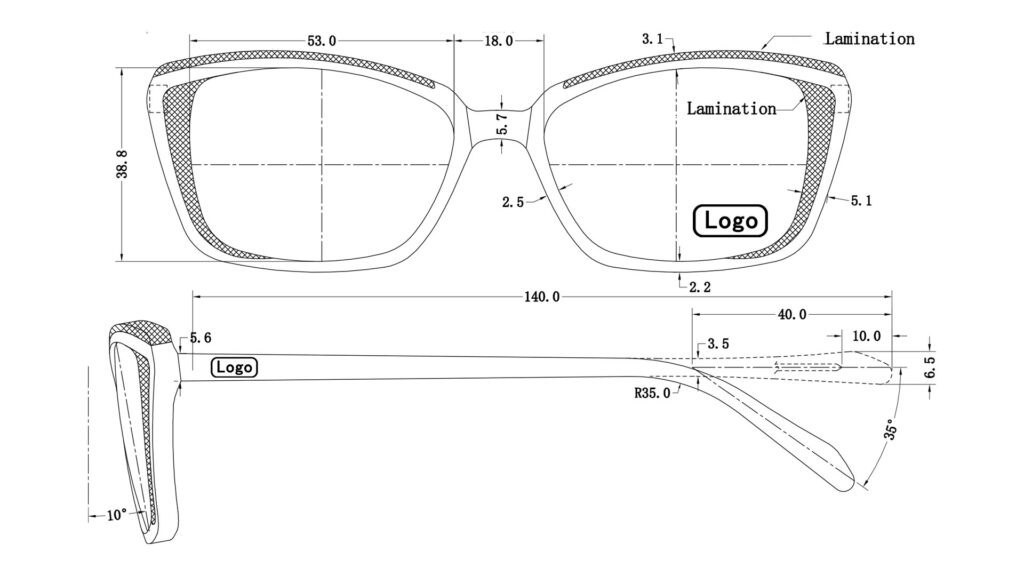
3. Selection of Production Process
Depending on the characteristics and requirements of the design, choose the appropriate modeling technique, such as 3D printing, CNC engraving, eyewear injection molds or hand-made samples.
4. Sample Quotation
Based on the finalized technical specifications of the eyewear or sunglasses, Ouyuan Eyewear will provide the clients with quotations for sample production, individual product quotations and minimum order quantities.
5. Production of Prototypes
An initial prototype of the eyewear is produced using the selected technology.
This stage may require several iterations to ensure that each component fits precisely and assembles well.
6. Assembly Adjustment
Assembles the components into a complete eyeglass frame.
The frame adjuster makes the necessary adjustments to the glasses to ensure that they are structurally stable and comfortable to wear.
7. Quality Check
Quality inspectors check the exterior quality, dimensional accuracy and functionality of the eyewear.
Ensure that there are no visible defects and that they conform to the design requirements.
8. Sending Samples of Eyeglasses
Samples are sent to the customer for confirmation after the samples are completed.
The speed of sending the samples depends on the choice of air or sea transportation.
9. Feedback and Improvement
If necessary, the design is fine-tuned (curved bends in the face of the frame, color adjustments, plating, etc.) based on feedback from test wearers.
The previous steps may be repeated until a satisfactory finished product is achieved.
10. Final Confirmation
After completing all adjustments, final quality control is performed.
After getting the final confirmation from the client, we can enter the mass production stage.
11. Mass production preparation
Develop a detailed production process according to the final confirmed samples, and production delivery date.
Prepare molds, tools and other production equipment.
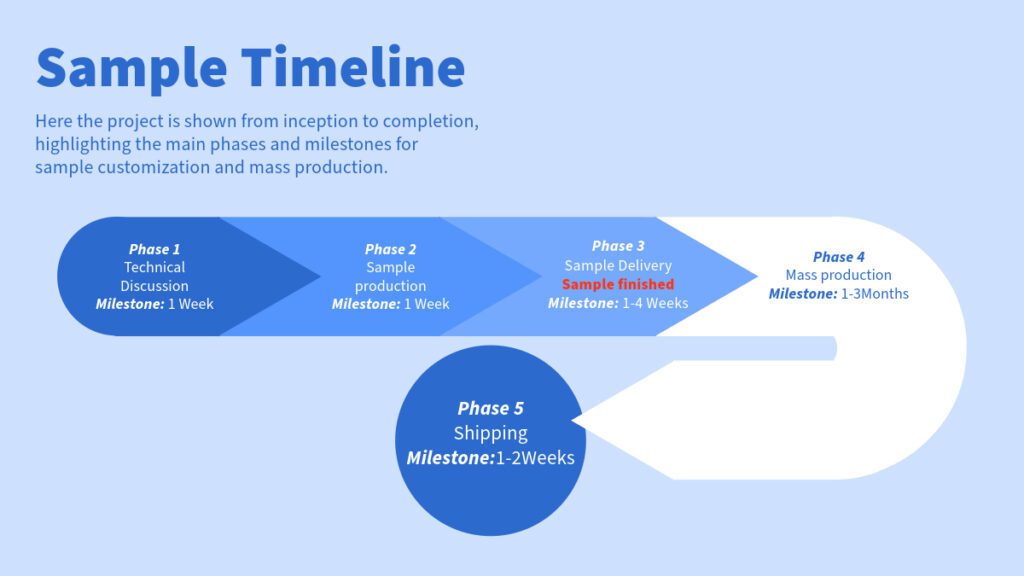
Conclusion
This process ensures that eyewear products meet the desired results and standards before mass production.
Notes:
*The cost of the eyewear sample will be different depending on the process and material.
*If you are purchasing products from our existing collection as samples, usually we will charge 10$ fee, if the sample price exceeds 10$ then we will charge according to the actual cost, once you place an order we will refund the sample fee.
*The sampling of eyeglasses cases and other accessories follows the above process, the manufacturer may be our cooperative factory or the eyeglasses case packaging factory that we invested in.